In the world of factory automation, few innovations have made as significant impact as Automated Guided Vehicles (AGVs). These high-tech machines are like little robots that move stuff around in factories, warehouses, and places where things need to be moved efficiently. They help make things faster, safer, and more organized. In this blog post, we’re going to talk about what AGVs are, how they do their job, where they’re used, how they make things safer, and the merits and demerits things about them.
What are Automated Guided Vehicles (AGVs)?
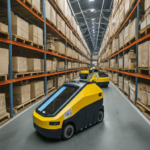
Automated Guided Vehicles (AGVs) are mobile robots used for material handling and transportation tasks in industrial settings. They are designed to navigate autonomously without the need for human intervention. AGVs follow pre-defined paths, often guided by various technologies such as magnetic strips, lasers, or GPS. Their primary purpose is to streamline workflows, reduce manual labor, and minimize the risk of human error in material transport.
How Do Automated Guided Vehicles Work?
AGVs operate using a combination of navigation technologies, sensors, and software. Here’s a closer look at the key components and functionalities:
1. Navigation Technologies:
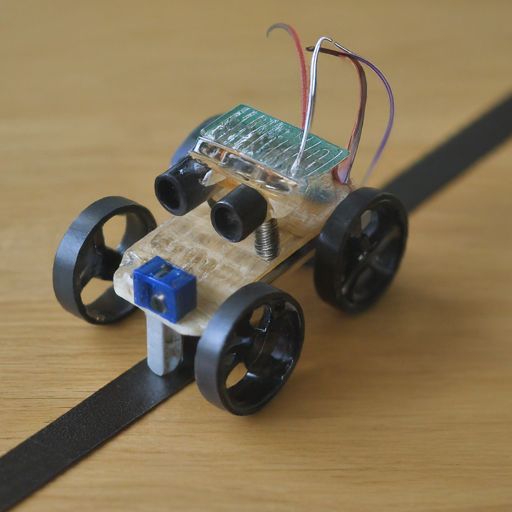
- Magnetic Strips/Tapes: Embedded on the floor, these guide the AGV along a specific path.Line following robot is the best example for it. In LFR(line following robot) infared sensor are used to identify the path of the robot.Click here to know more about line following robot.
- Laser Guidance: AGVs equipped with laser sensors reflect signals off targets placed in the environment to determine their location and navigate accurately.
- Vision Systems: Cameras and image processing algorithms enable AGVs to interpret their surroundings and follow visual cues.
- GPS/RTLS: For outdoor or large indoor spaces, GPS and Real-Time Location Systems (RTLS) help in precise navigation.
2. Sensors:
- Proximity Sensors: Detect obstacles in the AGV’s path to prevent collisions.
- Load Sensors: Ensure that the AGV can safely handle the material being transported.
- Environmental Sensors: Monitor the surrounding environment to adapt to changes or unexpected conditions.
3. Software:
- Fleet Management Software: Coordinates multiple AGVs, optimizing routes, schedules, and task assignments.
- Control Systems: Onboard computers that process sensor data and execute navigation and handling tasks.
Industrial Applications of AGVs
AGVs are used across various industries, including automotive, electronics, pharmaceuticals, and logistics. Common applications include:
1. Material Transport:
- Moving raw materials to production lines.
- Transporting finished goods to storage or shipping areas.
2. Assembly Line Integration:
- Delivering components and subassemblies to different stages of the production line.
3. Warehousing:
- Storing and retrieving items from high-density storage areas.
- Conducting inventory checks and stocktaking.
4. Distribution:
- Sorting and transporting packages in distribution centers.
- Loading and unloading goods from trucks and other transport vehicles.
How Do AGVs Increase Safety?
1. Reduced Human Involvement:
By automating material handling tasks, AGVs minimize the need for human workers in potentially hazardous environments, reducing the risk of workplace accidents.
2. Consistent Operation:
AGVs operate with precision and consistency, avoiding the variability and fatigue-related errors common with human workers.
3. Advanced Sensors:
Equipped with sophisticated sensors, AGVs can detect and avoid obstacles, ensuring safe operation even in dynamic environments.
4. Emergency Stop Mechanisms:
AGVs are designed with emergency stop features that can be activated to immediately halt operations in case of unexpected situations.
Also Read| Chatgpt API integration in c# app
Merits and Demerits of AGVs
Merits:
- Increased Efficiency: AGVs can operate 24/7 without breaks, significantly boosting productivity and operational efficiency.
- Cost Savings: Over time, AGVs reduce labor costs and minimize losses due to damage or errors in material handling.
- Flexibility: AGVs can be reprogrammed or re-routed to accommodate changes in production layouts or processes.
- Improved Accuracy: Precise navigation and handling capabilities reduce the likelihood of errors, enhancing overall process accuracy.
Demerits:
- High Initial Investment: The upfront cost of purchasing and implementing AGVs can be substantial, posing a barrier for smaller enterprises.
- Maintenance Requirements: Regular maintenance is essential to ensure AGVs operate smoothly, which can add to operational costs.
- Complex Implementation: Integrating AGVs into existing workflows requires careful planning and can be complex, especially in older facilities.
- Dependency on Technology: AGVs rely heavily on technology, making them vulnerable to issues such as software bugs or sensor malfunctions.
Automated Guided Vehicles represent a significant leap forward in industrial automation, offering numerous benefits in terms of efficiency, safety, and cost savings. While they come with challenges such as high initial costs and maintenance needs, the long-term advantages often outweigh these concerns.
Discussion (0)
Share Your Thoughts